In the field of power electronics testing, rack-mounted load bank, with its standardized design and flexible deployment capabilities, is widely used in laboratory research and development, quality inspection on production lines, and on-site operation and maintenance. However, the performance requirements for it vary significantly in different scenarios. Reasonable selection is the key to ensuring the test efficiency and data reliability.
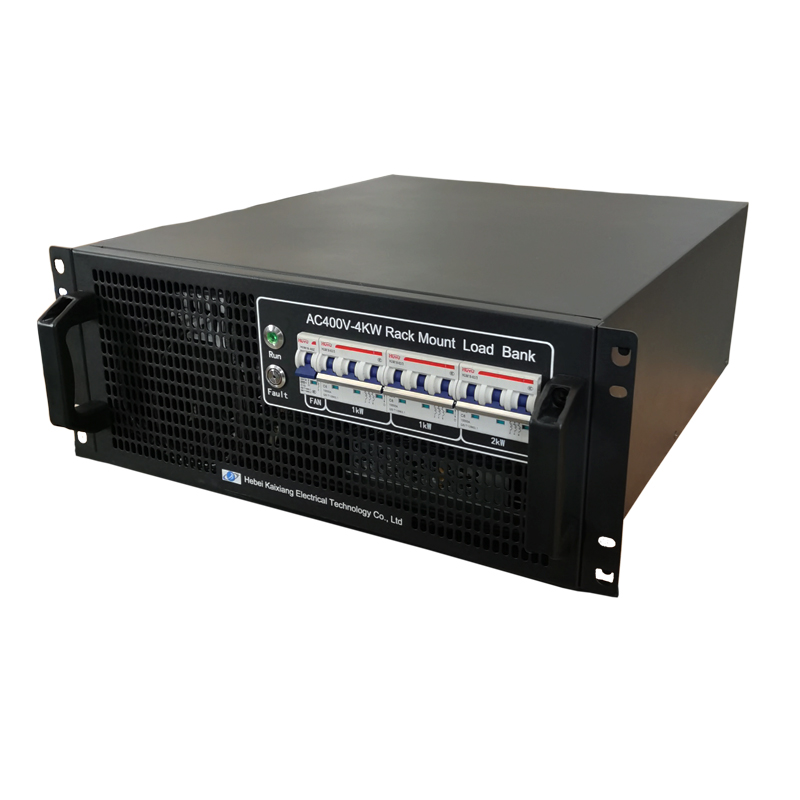
rack-mounted load Banks
Laboratory scenario: Equal emphasis on precision and flexibility
The laboratory focuses on the principle verification and performance optimization of the equipment. It is required that load bank support wide-range parameter adjustment (such as 0-1000V/0-500A) and high-precision measurement (±0.1% FS). It is recommended to choose 2U or 4U rack models, which integrate harmonic simulation and programmable waveform functions, and are compatible with Modbus/TCP or LabVIEW communication protocols, facilitating real-time data collection and analysis.
Production line scenario: Efficiency and stability take priority
The production line test emphasizes the connection between high repeatability and automation. The load bank needs to meet the requirements of 24×7 continuous operation and rapid switching of test programs. It is recommended to install a 4U or larger expansion rack, equipped with redundant heat dissipation and automatic diagnosis modules, and achieve "scanning code for immediate testing" through PLC or MES systems. The testing cycle of a single device should be controlled within 3 minutes.
On-site scene: Adapt to extreme environments
Outdoor or mobile tests require that load bank has the characteristics of wide-temperature operation (-40℃ to 70℃) and high protection (IP54+). The lightweight designed portable rack (such as 4U integrated 50kW) is equipped with a lithium battery power supply module, supporting offline data storage and 4G backhaul, balancing portability and functional integrity.
Core principles of selection
Power adaptation: A 20% margin should be reserved in the laboratory, and the production line needs to match the maximum load of the equipment.
Communication protocol: Give priority to supporting industrial standard protocols such as OPC UA and Modbus TCP;
Scalability: The modular design facilitates future functional upgrades (such as energy feedback modules).
From R&D verification to batch testing, the precise selection of rack-mounted load banks needs to be carried out around the scene characteristics. Through the adaptation of specification parameters and functional modules, the testing efficiency can be significantly improved and the full life cycle cost of the equipment can be reduced.