Generators, as core equipment for power supply, play a pivotal role in various application scenarios. However, during actual operation and testing, generators may encounter numerous performance issues. This article delves into the common problems encountered in generator performance testing and their solutions, aiding readers in better understanding and maintaining generator equipment.
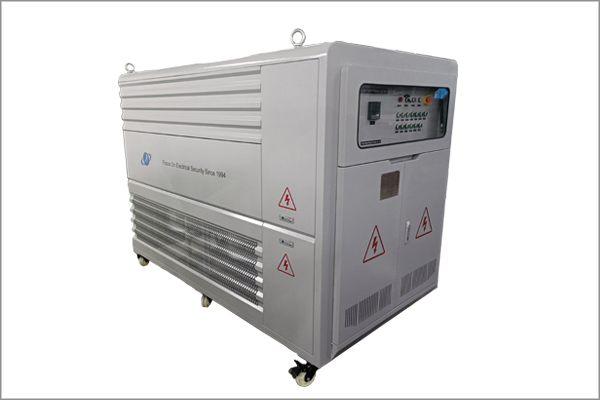
Load Bank for generator testing
I. Common Issues and Causes
1. Difficulty in Starting or Failure to Start
Causes:
Insufficient fuel supply, such as an empty fuel tank, clogged fuel filters, or air in the fuel lines.
Low battery charge or corroded battery terminals.
Starter motor malfunction.
Fuel depletion, overheating of cooling water, tripping of overload protection, or electrical faults.
Solutions:
Check and ensure the fuel tank is full, replace clogged fuel filters, and bleed air from the fuel system.
Charge or replace the battery, and test the starter motor.
Check fuel supply and cooling systems, and troubleshoot electrical and mechanical faults.
2. Output Power Below Rated Value
Causes:
Wear and tear of internal components, such as a broken governor spring.
Clogged fuel filters, resulting in insufficient fuel injection by the pump.
Poor fuel quality or clogged cooling systems.
Solutions:
Inspect and replace fuel filters to ensure adequate fuel supply.
Adjust governor parameters to ensure fuel supply and combustion efficiency.
Clean cooling systems to ensure effective heat dissipation.
3. Abnormal Noises During Operation
Causes:
Cooling system failures, such as a malfunctioning water pump or clogged radiator.
Inadequate ventilation or excessive load.
Worn mechanical components, such as damaged bearings.
Solutions:
Inspect and repair various components of the cooling system, ensuring adequate coolant and no leaks.
Optimize ventilation conditions and allocate loads reasonably.
Regularly inspect and replace worn mechanical components.
4. Excessive Body Temperature
Causes:
Aging or damaged seals, loose connections.
Failed cooling system or insufficient coolant.
Solutions:
Replace aging or damaged seals and tighten connections.
Inspect and repair the cooling system to ensure adequate coolant.
5. Unstable Voltage
Causes:
Faulty or aged voltage regulation devices.
Power supply issues or improper operation.
Solutions:
Inspect and repair voltage regulation devices to ensure power stability.
Standardize operating procedures to avoid misoperations.
II. Performance Testing Standards and Solutions
1. Voltage Regulation Testing
Standard:
Monitor the fluctuation range of the output voltage under no-load, 50% load, 100% load, and 110% overload conditions, which should remain within ±2% of the rated voltage.
Solution:
Use a voltmeter for monitoring, record and analyze data, and adjust the voltage regulation device to meet standards.
2. Frequency Stability Testing
Standard:
Measure the variation in output frequency under different loads, with the fluctuation range controlled within ±0.5 Hz.
Solution:
Use a frequency meter for measurement and adjust generator parameters to improve frequency stability.
3. Power Output Testing
Standard:
Apply rated load and record the actual output power, which should be within ±5% of the rated power.
Solution:
Use power measurement equipment for measurement and adjust generator parameters to improve power output efficiency.
4. Insulation Resistance Testing
Standard:
Measure the insulation resistance between the windings and ground using a megohmmeter, with the minimum acceptable value typically set at 10 MΩ.
Solution:
Perform insulation resistance testing and replace components with unqualified insulation performance.
5. Vibration and Noise Testing
Standard:
The vibration amplitude should be below the specified limit (e.g., 2 mm/s), and the noise level should not exceed 85 dB.
Solution:
Use vibration sensors and noise meters for measurement, optimizing generator design and installation location to reduce vibration and noise.
III. Conclusion and Recommendations
Common issues in generator performance testing involve starting, operational stability, emissions, cooling systems, and voltage regulation, among others. To ensure the normal operation and extended service life of generators, regular maintenance and prompt troubleshooting are required. Here are some recommendations:
Regularly conduct no-load and load tests on generators to ensure they can reliably start and supply power when needed.
Follow the maintenance intervals recommended in the user manual or by the manufacturer to change oil and oil filters, keeping the engine lubrication system clean and effective.
Regularly check coolant levels and quality, clean radiators, and ensure the cooling system is free of leaks and clogs.
Use high-quality fuel, regularly replace fuel filters, and prevent fuel system clogging and contamination.
Regularly check battery charge and connection status, keep the battery clean, and ensure the generator can start smoothly.
Perform preventive maintenance on generators regularly to identify and resolve potential issues promptly.
In summary, the common issues and solutions in generator performance testing require comprehensive consideration of factors such as equipment design, operating environment, and maintenance management. By strictly adhering to performance testing standards and adopting targeted maintenance measures, the stable operation and efficient performance of generators in various application scenarios can be ensured.